Accessory machines
I.C.M.I. Industrial Furnaces, thanks to the many years of experience gained in heat treatments, designs and manufactures accessory machines, identifying itself as a competent and aware referent for the supply of complete and automated systems at the service of an entire process.
Quenching and solubilization tanks
Water, water and polymer and oil quenching and solubilization tanks.
The quenching and solubilization tanks consists of a sturdy metal structure painted with epoxy paint to increase the oxidation resistance. The tank is fitted with a relief level system to keep the fluid level constant. In case of oil quenching and solubilization, the tank can be provided with a second skin, i.e. a second reservoir to avoid any possible oil leakage.
The quenching and solubilization tanks can be equipped with all the necessary systems needed for the right implementation of the desired treatment.
In particular, the tanks can be equipped with:
- Fluid reconditioning system
- Mechanical stirring system
- Scale removing system
- Exhausts / oil vapours extraction system for the oil quenching and solubilization tanks
- Fire-fighting system for oil quenching and solubilization tanks
- Fluid treatment system, entirely mounted on a skid.
To deposit the charge and realize its complete immersion, both crane bridges structures or incorporated descenders, can be used to deposit the charge and realize its complete immersion.
The tanks with their ancillaries are designed and manufactured based on the functional specifications of the entire line of which, thanks to the automation, are an integrated element.
Tank descenders
Descenders for the deposit / removal of the components to be treated.
Usually the descenders are metallic carpentry structures designed to support the loads at stake and to allow the immersion and lifting of the material in the tank.
They are moved either by an oleo-dynamic / hydraulic system or by an electromechanical system.
The descenders are designed and manufactured based on the functional specifications of the entire line of which, thanks to the automation, are an integrated element.
Charging machines
To serve the plants, dedicated loaders are realized with the aim to comply any operational requirement.
The ancillaries charging machines are divided into two main categories: bridge loaders and grounded loaders.
Bridge loaders
This type of loaders are bridge shaped or are designed to take advantage of aerial runways. To grab the material to be treated, they can integrate a gripper, L or C shaped forks being able to adapt to the geometries at stake. This kind of loaders can also be realized with detachable forks I order to reach higher levels of flexibility of the plant.
Grounded loaders
The grounded loaders are loaders with wheels sliding on rails equipped with forks for picking up / depositing the charge. For heavy and onerous loads, the charging machines are stabilized thanks to a third row of anti-overturning rails in order to guarantee the safety and reliability of the machine in every situation.
The typical movements of the loaders are:
- Longitudinal translation along the runways to move along the entire designated system, usually achieved by means of gearmotors under inverters for easy management of the acceleration / deceleration ramps;
- Transversal translation (along the axis of the bridge or base structure) for the positioning of the material to be treated, usually carried out using gearmotors under inverter for easy management of the acceleration / deceleration ramps;
- Vertical translation for picking up / depositing the charge by means of electromechanical, pneumatic or oleo-dynamic / hydraulic systems according to the design needs;
- Rotations up to 270 ° achieved thanks to the use of motorized fifth wheels.
The loaders are designed and manufactured based on the functional specifications of the entire line of which, thanks to the automation, are an integrated element.
Quenching heads
The quenching heads are dedicated typically to “single bar/ single tube” lines.
They are a carpentry structure of geometry variable basing on the pieces to be treated, in which appropriate nozzles are installed to emit cooled pressurized water.
The quenching heads are designed and manufactured based on the functional specifications of the entire line of which, thanks to the automation, are an integrated element.
Atmosphere generators
The atmosphere generator are machines realized to generate a protective atmosphere needed to specific types of treatments. The percentage composition of the atmosphere is settable between certain ranges so that it can be possible to obtain a gas mixture with the right reducing component .
This is possible managing the parameter :
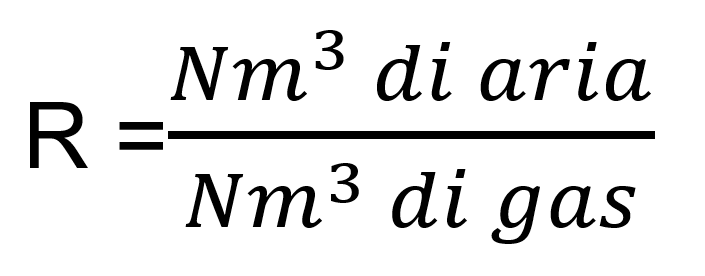
- The combustion chamber to generate the gas, equipped with all the needed instrumentation;
- A cooler in order to refrigerate the gas avoiding further modification in the chemical composition and in order to condensate the vapour inside the combustion products themselves;
- The condensation drain siphon.
The atmosphere generators are designed and manufactured based on the functional specifications of the entire line of which, thanks to the automation, are an integrated element.
Other ancillary machines
In order to provide complete and functional systems, I.C.M.I. Industrial Furnaces has also gained experience in the design and construction of:
- Loading and unloading or transfer trolleys, shuttle-type motorized stalls;
- Fixed deposit or buffer stalls;
- Tilters;
- Singulators, distributors and unloading cradles for bars / pipes;
- Cooling chambers